The Automotive market has been Trexel’s core industry since our beginning, and there have been thousands of automotive parts realized in commercial production with MuCell® technology.
Overall Vehicle Weight Reduction and Improved Fuel Economy
The Trexel complete process solution provides a lighter and more accurate plastic part at lower production costs. Trexel’s foaming solutions process enables automotive components manufacturers to lightweight plastics parts for overall vehicle weight reduction and improved fuel economy.
Part costs are typically reduced by 10 to 20% as a result of lower material consumption, shorter molding cycle times and reduced machine clamping tonnage requirements.
The uniform parts shrinkage and substantially reduced stress in the molded part lead to predictable and repeatable part geometry, allowing for the use of lower cost polyolefin resins without warpage or distortion in the part.
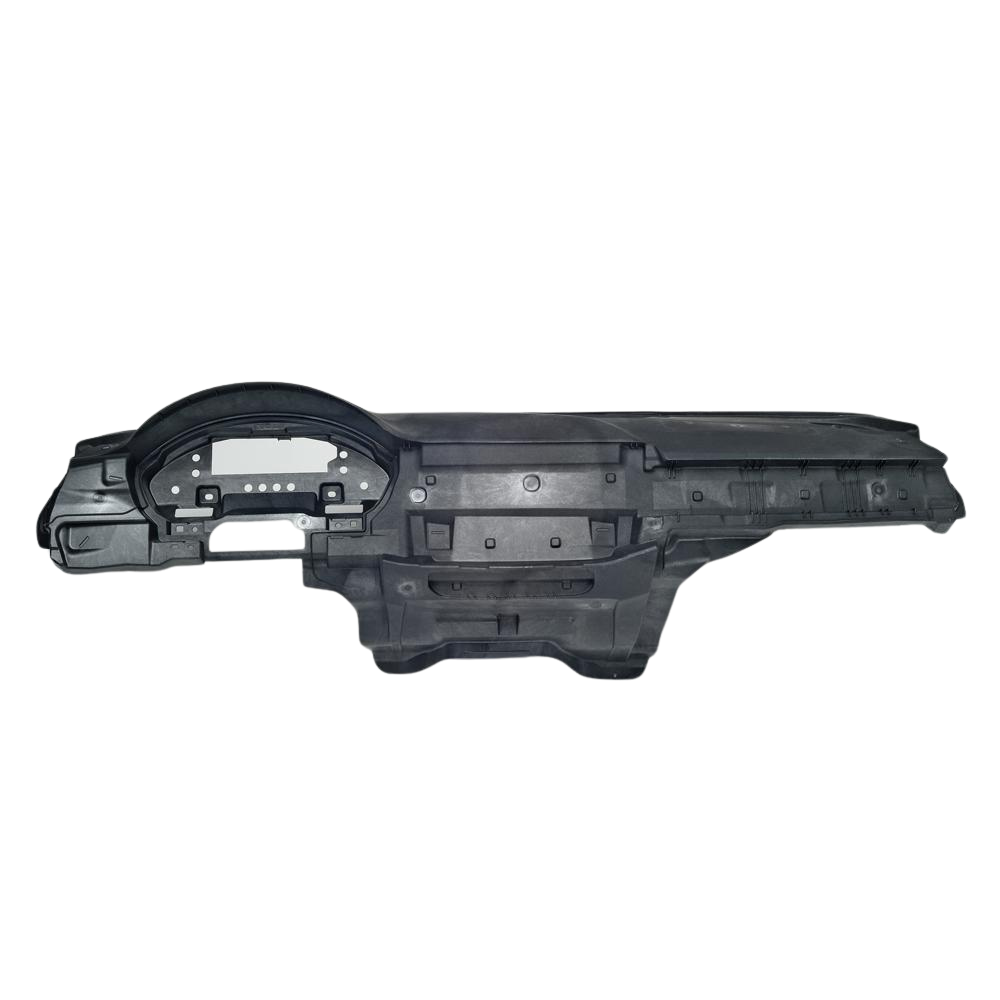
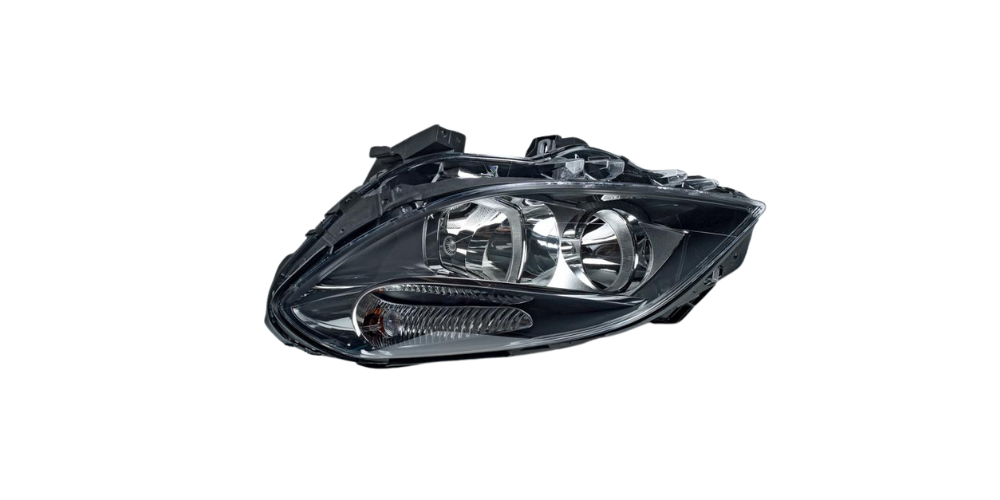
Design For Functionality Without Plastic Process Limitations
To be a leader in the Automotive industry, you need customizable options and flexibility for your parts. By replacing the traditional pack and hold phase of the solid molding process with cell growth, Trexel’s foaming solutions allow for uniform and locally applied pack pressure through cell growth, which allows part design to be optimized with material thickness in those areas that require strength and reduced wall thickness in areas that are not structural.
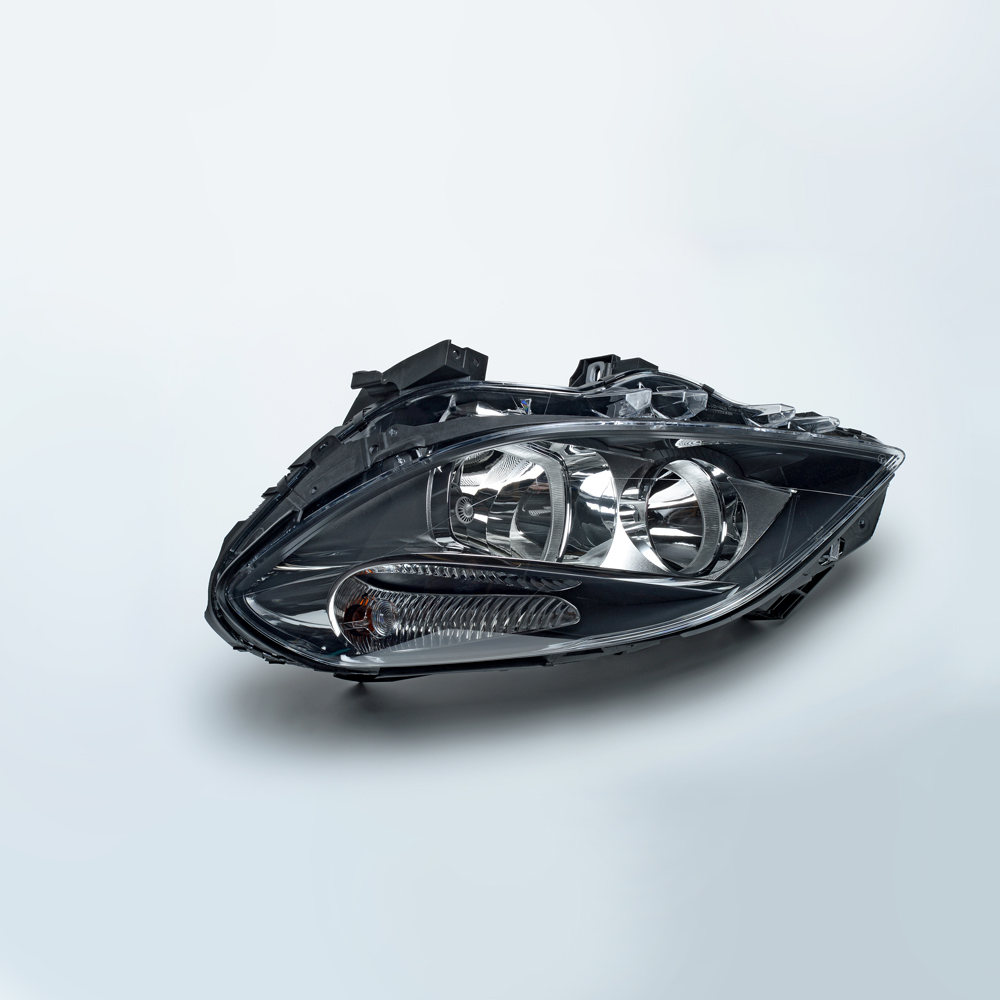
Design For Functionality Without Plastic Process Limitations
To be a leader in the Automotive industry, you need customizable options and flexibility for your parts. By replacing the traditional pack and hold phase of the solid molding process with cell growth, Trexel’s foaming solutions allow for uniform and locally applied pack pressure through cell growth, which allows part design to be optimized with material thickness in those areas that require strength and reduced wall thickness in areas that are not structural.
Cost and Processing Advantages
Consumer
Consumer
Trexel delivers some unique advantages to the consumer goods industry beyond just cost reduction, design freedom, and sustainability. MuCell® enables manufacturers to produce lightweight products without compromising strength and durability.
Electronics
Electronics
Trexel’s microcellular foaming technology has been used in paper path components for copiers and printers for the past 20 years. Adoption has primarily been driven by improvements in dimensional stability which is critical to movement of the paper through the device and print quality.
Footwear
Footwear
Trexel has been at the forefront of foaming applications to facilitate the conversion from established EVA chemical foaming processes to the use of thermoplastics TPU physical foaming for the production of shoe mid-soles.
Industrial
Industrial
Trexel’s foaming technologies are used in many diverse industrial applications from shipping pallets to crates to buckets, to power tools and more.
Medical
Medical
Plastics play a major role in healthcare, especially in the manufacturing of large and small medical devices. Trexel’s lightweighting technology has become more and more important to the industry.
Packaging
Packaging
Trexel’s P-Series MuCell® system is specifically designed to meet the unique processing demands of brand owners striving to meet cost reduction and sustainability goals.
Let’s Make it Happen
Don’t hesitate to reach out to our global team.
We’re here to assist and provide you with answers to all of your inquires. Let’s take a look at your application and discuss whether our technology can help you reduce costs AND your carbon footprint. We are eager to guide you through the process. Get in touch today!
By Phone:
781-932-0202
By Email:
info@Trexel.com