Trexel’s foaming technologies are used in many diverse industrial applications from shipping pallets to crates to buckets, to power tools and more. MuCell® uses a microcellular injection molding technique that introduces tiny gas bubbles into plastic during the molding process. These bubbles create a cellular structure with the plastic, resulting in lighter, and more cost-effective products.
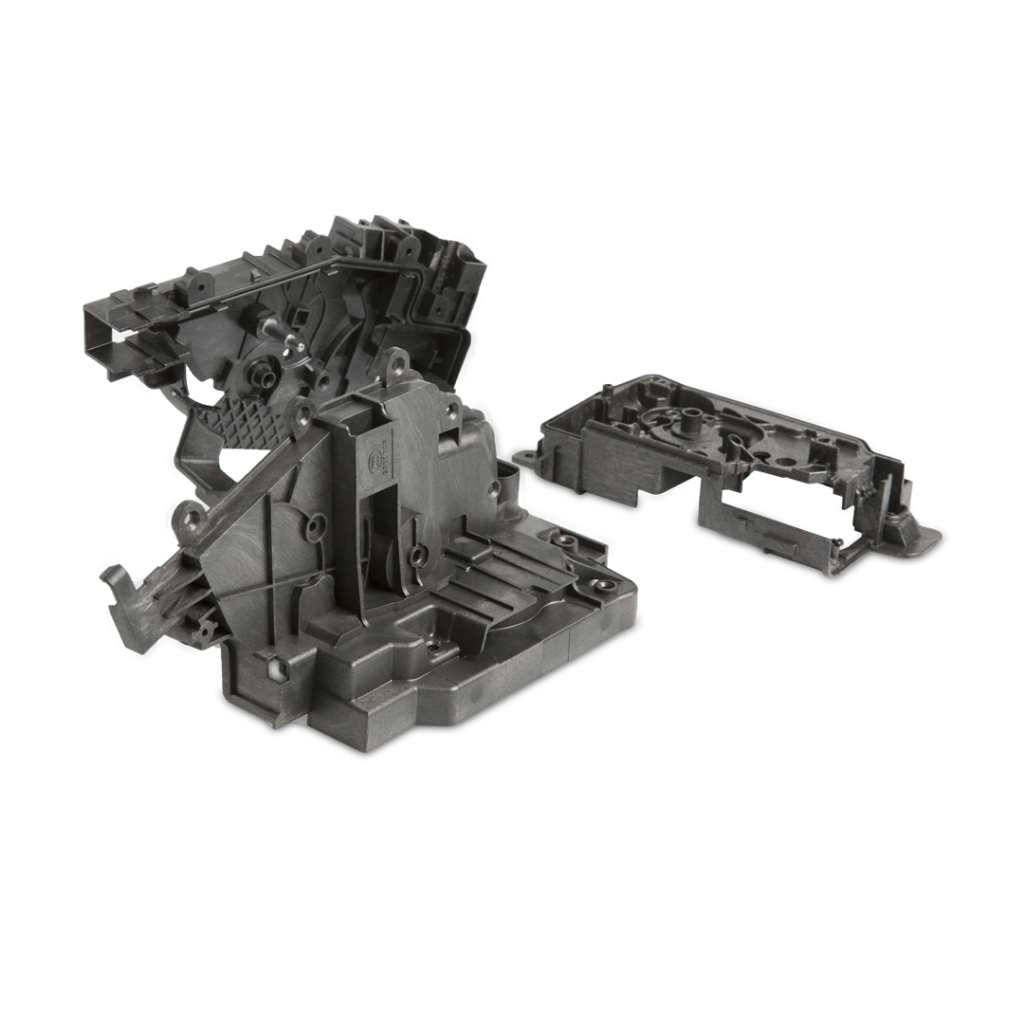
Push Design Boundaries and Reduce Waste
Engineers and manufacturers are embracing this technology for its ability to optimize product performance while reducing the environmental impact. MuCell® is enabling businesses to push the boundaries of design while reducing waste. Manufacturers can produce more parts in less time, leading to cost saving and improved overall productivity. The microcellular structure opens up new design possibilities for engineers and product designers and allows for intricate and complex shapes to be molded with precision.
Cost Savings and Increased Sustainability
The introduction of the microcellular structure in plastic allows for faster cooling and solidification during the molding process. This reduces cycle times leading to higher production rates. By reducing the plastic material for each part, without compromising strength in many cases, MuCell® provides cost savings and increased sustainability.
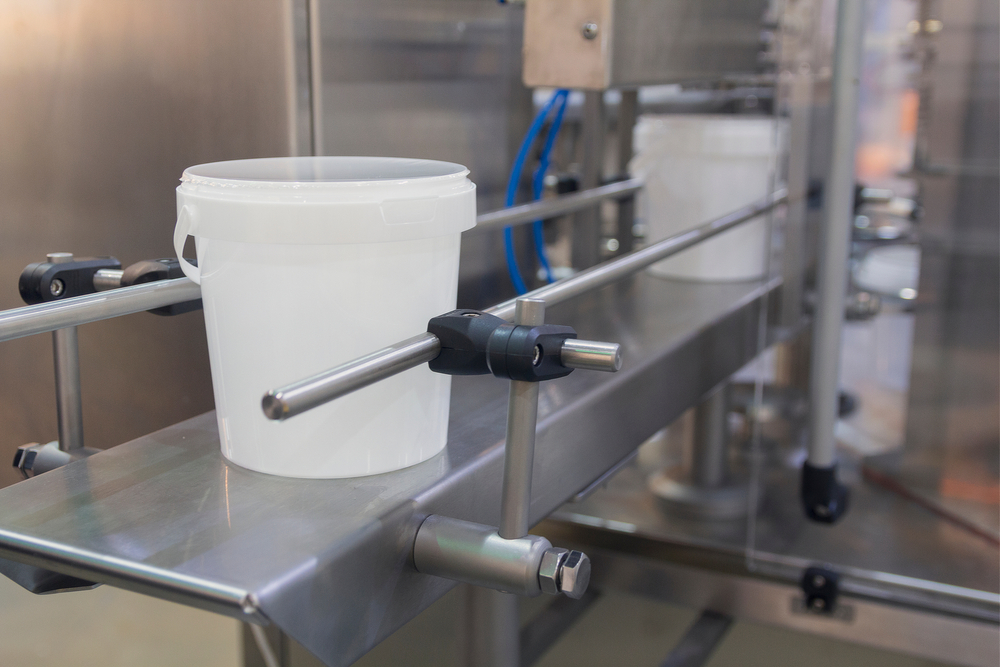
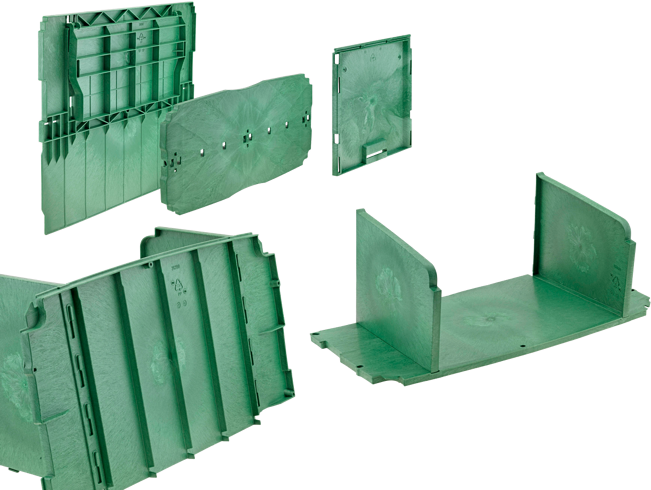
Compatible With A Wide Range of Materials
The MuCell® process offers a high degree of dimensional stability which provides for improved fit and assembly for enclosures, improved flatness for gears and the ability to eliminate vacuum voids/shrink voids in thicker cross sections.
The unique nature of physical foaming processes are that they do not rely on a chemical reaction to create the foaming gas and unlike endothermic chemical foaming agents there is no water present as a by-product that can react with moisture sensitive resins. As such, the MuCell® process is compatible with a wide range of materials from biopolymers that have lower process temperatures, 160 to 180 C, and are highly reactive with moisture to materials such as PEI, PEEK and PSU which can have process temperatures in excess of 380 C.
Cost and Processing Advantages
Automotive
Automotive
Automotive has been Trexel’s core industry since our beginning, and there have been thousands of automotive parts realized in commercial production with MuCell® technology.
Consumer
Consumer
Trexel delivers some unique advantages to the consumer goods industry beyond just cost reduction, design freedom, and sustainability. MuCell® enables manufacturers to produce lightweight products without compromising strength and durability.
Footwear
Footwear
Trexel has been at the forefront of foaming applications to facilitate the conversion from established EVA chemical foaming processes to the use of thermoplastics TPU physical foaming for the production of shoe mid-soles.
Electronics
Electronics
Trexel’s microcellular foaming technology has been used in paper path components for copiers and printers for the past 20 years. Adoption has primarily been driven by improvements in dimensional stability which is critical to movement of the paper through the device and print quality.
Medical
Medical
Plastics play a major role in healthcare, especially in the manufacturing of large and small medical devices. Trexel’s lightweighting technology has become more and more important to the industry.
Packaging
Packaging
Trexel’s P-Series MuCell® system is specifically designed to meet the unique processing demands of brand owners striving to meet cost reduction and sustainability goals.
Let’s Make it Happen
Don’t hesitate to reach out to our global team.
We’re here to assist and provide you with answers to all of your inquires. Let’s take a look at your application and discuss whether our technology can help you reduce costs AND your carbon footprint. We are eager to guide you through the process. Get in touch today!
By Phone:
781-932-0202
By Email:
info@Trexel.com