Learn here how to take advantage of new lightweighting and recycle utilization opportunities in consumer packaging, thanks to a collaboration of leaders in microcellular foaming and multilayer head design.
#sustainability
This article was original published on Plastics Technology, PTOnline.com.
Written by Sam Dix, Director of R&D.
Use of recycled plastics materials is a critical factor in the move toward a fully closed-loop economy in the plastic industry. Simply put, producers must reduce their energy and raw-material consumption to meet strict new legislation touted for introduction in 2025, as laid out in the proposed packaging regulation published in November 2022 by the European Commission. Cosmetic products that are contact-sensitive, for example, will contain 40% postconsumer regrind (PCR) and all other bottle packaging will contain 35% and 65% by 2030 and 2065, respectively. This is a tall order.
The challenge is not only the supply, availability and quality of recycled resins but also the development of new processes to enable their use and exploit their potential. With the sudden requirement for PCR and the need for respectable quality, cost will likely be an issue. Brand owners, in particular, are looking for ways to remain cost-competitive with the virgin product configurations of today’s common packaging specifications. Lightweighting through foaming has also gained growing attention and process adoption in recent years as an alternative to downgauging, which may compromise topload performance.
Expert Partnership Facilitates Adoption
Trexel, a market leader in foaming technologies for lightweighting, and W. Müller, a market leader in blow molding multilayer head design, have partnered to create a lightweighting solution for inclusion of PCR and lowering the cost of bottle production without significantly sacrificing mechanical properties. Trexel has been delivering both physical and chemical foam lightweighting solutions for injection and blow molding. Its MuCell physical foaming technology is now standard or optional on many OEM injection molding platforms. With a recent focus on packaging solutions in injection molding, plus the company’s history of foaming blow-molded automotive ducts with the accumulator-head process, Trexel has implemented a MuCell foaming solution for extrusion blow molding (EBM) on shuttle and wheel machinery. Trexel is now working with brand owners on scale-up bottle projects.
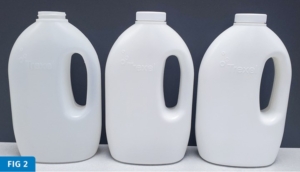
The multilayer solution involves metering nitrogen into the barrel of the EBM machine and foaming the core layer of a three-layer sandwich such that the layer ratio (by thickness) remains similar to the solid predecessor three-layer design but with reduced weight in the PCR core. There is also reduced core extruder speed associated with a given volumetric bottle output. By specifically coupling the MuCell process with a proprietary patented additive, impact strength, topload and ESCR will pass the necessary industry tests. Typically, there has been an improvement of up to 3 times in impact performance over previous foaming technologies, which is driving the ability to make larger foam-core bottles. The system and method are license-free and may be retrofitted to the existing screw and barrel, as depicted in Fig. 1. In addition to weight savings, TiO2 and other white masterbatches can often be reduced or eliminated, because foam adds an opaque appearance, as shown in Fig. 2.
Lightweighting through foaming is an alternative to downgauging, which may compromise topload performance.
W. Müller’s multilayer head and extruder systems can be retrofitted to most monolayer systems as well as on a new system. W. Müller, which built its first three-layer head in 1990, brings significant process experience with PCR-laden products through its RECO head series. MuCell is a physical foaming process, depending partially on the pressure events in the head or multiple heads in structure of three or more layers. As noted by Jens Schlueter, president of W. Müller USA, “Although there are many standard three-layer extrusion head designs out in the market, it is essential to have the experience with how to create designs that accommodate the foaming process. Understanding melt flow, melt pressure and how to perfectly dimension the flow channels inside the head is critical to a successful foaming application. Our expertise in providing custom-designed heads for different materials and designs ensures that our customers get the right solution for their needs and particular specifications.”
Of particular importance to the process is the ability of the Trexel SCF (supercritical fluid) delivery system to respond to pressure fluctuation that may arise from the addition of some lower-grade PCR to the extruder. Trexel’s proprietary system will “learn” process patterns and react to real-time events to keep foaming levels consistent to ensure process stability and consistent bottle geometry. To enable this, simple process timing signals from the blow molding machine are used.
W. Müller has installed two lab foaming systems, one at its headquarters in Troisdorf, Germany, and the second at its U.S. office in Agawam, Mass. They are both equipped with Trexel’s latest B120 SCF delivery system and handled bottle mold for use in demonstrations. Clients may also pick from other standard molds or supply their own molds to test out the technology.
Of particular importance is the ability of the gas-injection system to respond to pressure fluctuation that may arise from addition of some lower-grade PCR to the extruder.
To retrofit the pumping system, a hole is drilled in the existing barrel in a position so there is enough residence time to dissolve nitrogen gas in the melt. Trexel has conducted background research to mathematically define the exact parameters required to ensure homogeneous gas diffusion in such processes through work with its recently patented injection molding screw designs. Because almost 10 times less gas is used in the foam blow molding process than in injection molding, there is usually enough residence time to mix gas with the existing blow molding screw design, and therefore the process will not typically require a new screw and barrel.
It is anticipated that in the future Trexel’s SCF delivery system controls will be integrated into the W. Müller control system to provide a one-stop foaming add-on which will convert an existing monolayer system to a full multilayer foam system.
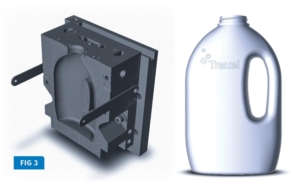
Case Study: Topload & Drop Impact
The following case study was used to corroborate and summarize recent work using the demonstration mold. A blow molding system was configured as in Fig. 2 and combined with Trexel’s handled bottle mold as shown in Fig. 3. The die tooling was downsized such that the parison layflat dimension was the same for solid and foamed extrudate – yielding the same amount of flash/top/tail. In some cases, die ovalization may change slightly from that for a solid product.
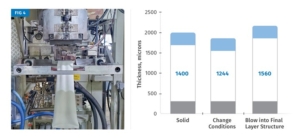
Weight was then reduced in the core extruder, as shown in the center bar in Fig. 4; here the tail was too short to actually mold a product. Gas was then injected and the structure was foamed back to a thickness similar to a solid part, as shown on the right-hand bar of Figure 4. Given that stiffness is a key factor that varies as a cube function of nominal thickness, overall thickness can be manipulated to offset the reduction in density, which varies only linearly with stiffness. In essence, foam has a better stiffness-to-weight ratio than solid structures.
Blow pressure was then applied, typically lower than for solid molding, sometimes in multiple stages. The lower pressure at these thicknesses does not introduce the need for greater cooling time or a change in mold venting. In the process, minor calibration or crushing of the structure takes place to leave the final product as shown in Fig. 5. For example, the final foam parison from Fig. 4 is 2.16 mm, which is calibrated (compressed) by nearly 50% during the blow process to leave a final thickness of 1.12 mm, shown in Fig. 5.
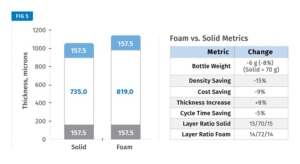
The result was a foamed bottle that is 6 g lighter, with an overall density of 0.830 g/cc and a core density of 0.760 g/cc. Nominal thickness of the outside layer was the same as in the solid structure, and extra thickness to maintain stiffness came from the foamed layer. The cycle time in this instance was reduced by 2.5 sec. The final metrics of the bottle are shown in the table in Fig. 5, which notes savings in bottle weight, cost and cycle time. It should be noted there are multiple ways to quantify the savings. Cycle time may remain constant (same volumetric output) but with reduced material consumption; or alternatively there might be similar material (weight) throughput as with a solid wall, but with increased volume output — more bottles per hour. In this case study, it was a mixture of both.
An important factor in the technology, as noted, is the homogeneous mixing of gas, but also the synergy of the gas desorption at the instant that pressure is released at the die exit. This creates very small bubbles with an aspect ratio typically no more than 2:1 and cell size less than 100 microns after blowing (Fig. 6). The foam parison continues expanding such that there is ample thickness in the base of the bottle. Unlike traditional nucleating agents, the proprietary nucleant additive in this process does not negatively affect impact strength (if, for example, you were to put it in an unfoamed product). The combination of those factors enables the foam technology to apply to much larger bottles than just 200 ml and pass impact tests.
Three base tests were performed on the test bottle. The drop-impact test was 11.5 ft for the foamed bottle with an ESCR test pass. Topload test results showed that for the same weight (comparing Trials 8 and 11 in Fig. 7), force per mm of thickness was the same for foamed and unfoamed bottles. Furthermore, the foamed bottle showed a 20% increase in total energy absorbed before the peak topload was reached.
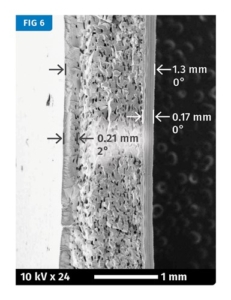
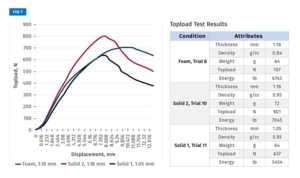
Further work is now being conducted on different materials and shapes for brand owners. This extends to biopolymers, which will not be subjected to the regulations in Europe when they begin to roll out but would benefit from cost reduction. Work is also being conducted on wheel machines where the technology has been run successfully at full scale on larger bottles for applications like household detergents.
Trexel has shown a new and improved way to foam bottles with the ability to reduce the cost of PCR-laden bottles and/or simply to lightweight bottles as an alternative to downgauging which is limited by topload strength. Foam has an improved stiffness-to-weight ratio and provides opacity without adding masterbatch.
Ability to pass topload and drop-impact tests enables foaming to be used in much larger bottles.
Trexel has addressed a key shortcoming of previous renditions of the foaming technology — in particular, drop-impact resistance has been addressed, while topload strength can be maintained by increasing thickness at the foamed lower density. Foaming will not be suitable for every product, such as monolayer, very thin, heavily embossed or with ultrahigh drop-impact requirements. But the list of successful applications is ever growing and gaining attention.
Foaming can be retrofitted to old machines or installed as new. In the former instance, W. Müller and Trexel have partnered to provide the ability to change a monolayer machine to make multilayer foam structures with minimal capital investment and no royalties.