MuCell® technology, also known as microcellular foam injection molding, is an innovative manufacturing process used to produce lightweight and cost-effective plastic parts. It involves the injection of a supercritical fluid (SCF), typically nitrogen or carbon dioxide, into the molten plastic during the molding process. This creates a microcellular foam structure within the plastic part, resulting in various benefits and highly accurate dosing. The latest evolution of MuCell® foaming features a smart, simple user interface with highly accurate dosing capability.
T-Series
Model | T-100 | T-200 | T-300 |
---|---|---|---|
Plasticizing Screw¹ | 18-60mm | >40-90mm | >70-120mm |
Shot Size | 10-40gr | >120-600gr | 600-3000gr |
Minimum Supply Pressure | 13.8 bar | 13.8 bar | 13.8 bar |
Maximum Supply Pressure | 200 bar | 200 bar | 200 bar |
Overall Dimensions (WxDxH) | 56x61x130cm | 56x79x156cm | 56x79x156cm |
Weight | 126kg | 195kg | 216kg |
Electrical Connection | 230/110 VAC 1Ø 50/60Hz | ||
Screen Size | 10″ (4:3) | 15″ (16:9) | 15″ (16:9) |
1 Guidelines Only. Please refer to the chart in brochure when considering the N2 dose and screw recovery time for appropriate model selection.
CO2 Option: Configures gas components with the capability to process CO2 and N2
Nitrogen Purity Control Option: Monitors purity of the nitrogen supply
Dual Bottle Option: Automatic nitrogen bottle switch station from 2 gas sources (not available with T-100)
P-Series
Model | P-300 |
---|---|
Plasticizing Screw* | up to 60mm |
Min SCF Dose (N2) | 100 mg |
Max SCF Flow Rate² | 400mg/sec |
SCF Delivery System
Overall Dimension (WxDxH) |
55x79x155cm |
Electrical Connection | 230/110 VAC 1Ø 50/60Hz |1.6A |
Compressed Air Consumption | 6.2 bar – 2250 NL/h – 10mm |
Max Length Kit “A” | 6m |
Max Length Kit “B” | 0.9m (3ft) | (>D40 1,2m (4ft)) |
P-Series Dosing Module
Overall Dimensions (WxDxH) |
24.8×47.4x27cm |
Weight | 10.6kg |
¹ Guidelines Only. For application specific systems selection, please contact Trexel.
² Based on expected 1 year service lifetime.
B-Series
Model | B-100 | B-120 | B-300 | B-320 |
---|---|---|---|---|
Operating Mode | Discontinuous Flow | Continuous
Flow |
Discontinuous
Flow |
Continuous
Flow |
Minimum Supply Pressure | 13.8 bar | 13.8 bar | 13.8 bar | 13.8 bar |
Maximum Supply Pressure | 200 bar | 200 bar | 200 bar | 200 bar |
Maximum Output Pressure | 350 bar | 350 bar | 350 bar | 350 bar |
Overall Dimensions (WxDxH) | 56x61x130cm | 56x61x130cm | 56x63x136cm | 56x63x136cm |
Weight | 126kg | 126kg | 240kg | 240kg |
Screen Size | 10″ (4:3) | 10″ (4:3) | 15″ (16:9) | 15″ (16:9) |
Signal Connection | Screw Rotation Accumulator Position |
Screw Rotation Mold Close | Screw Rotation Accumulator Position |
Screw Rotation Mold Close |
Electrical Connection | 230/110 VAC 1Ø 50/60Hz |
NC-250/NC-500
Model | NC-250 | NC-500 |
---|---|---|
Capacity | 215 l/min | 500 l/min |
Intake Pressure | Atmospheric | Atmospheric |
Intake Temperature | +5*C…+45*C | +5*C…+45*C |
Working Pressure | 300-330 bar | 365 bar |
Maximum Pressure | 365 bar | 365 bar |
Power Consumption at Max Pressure | 4.7 kW | 10.2 kW |
Operating Voltage | 400V | 400V |
Frequency | 50 Hz | 50 Hz |
Energy Efficiency | IE 3 | IE 3 |
Overall Dimensions (WxDxH) | 1380x830x1520mm | 1480x830x1520mm |
Weight | 290kg | 350kg |
Satellite Dosing Unit
Model | T-S01 | T-S00 | P-S00 |
Plasticizing Screw Size | 18-45mm | 40mm + | Any |
Shot Size Range¹ | Below
140g |
Above 120g | Any |
Minimum SCF Dose (N2) | 60 mg | 600 mg | 100 mg |
Maximum Discharge Pressure | 345 bar | 345 bar | 345 bar |
Satellite SCF System Dimensions, cm (WxDxH) | 50.2×65.1×127 | ||
Weight | 102 kg | ||
Electrical Connection | 230/110 VAC 1Ø 50/60 Hz 1.6A | ||
Compressed Air Consumption | 6.5-10 bar – <15 NL/min – 10mm | ||
SCF Gas Connection | 17,2 – 200 bar – 8mm |
¹Guidelines Only. For application specific systems selection, please contact Trexel.
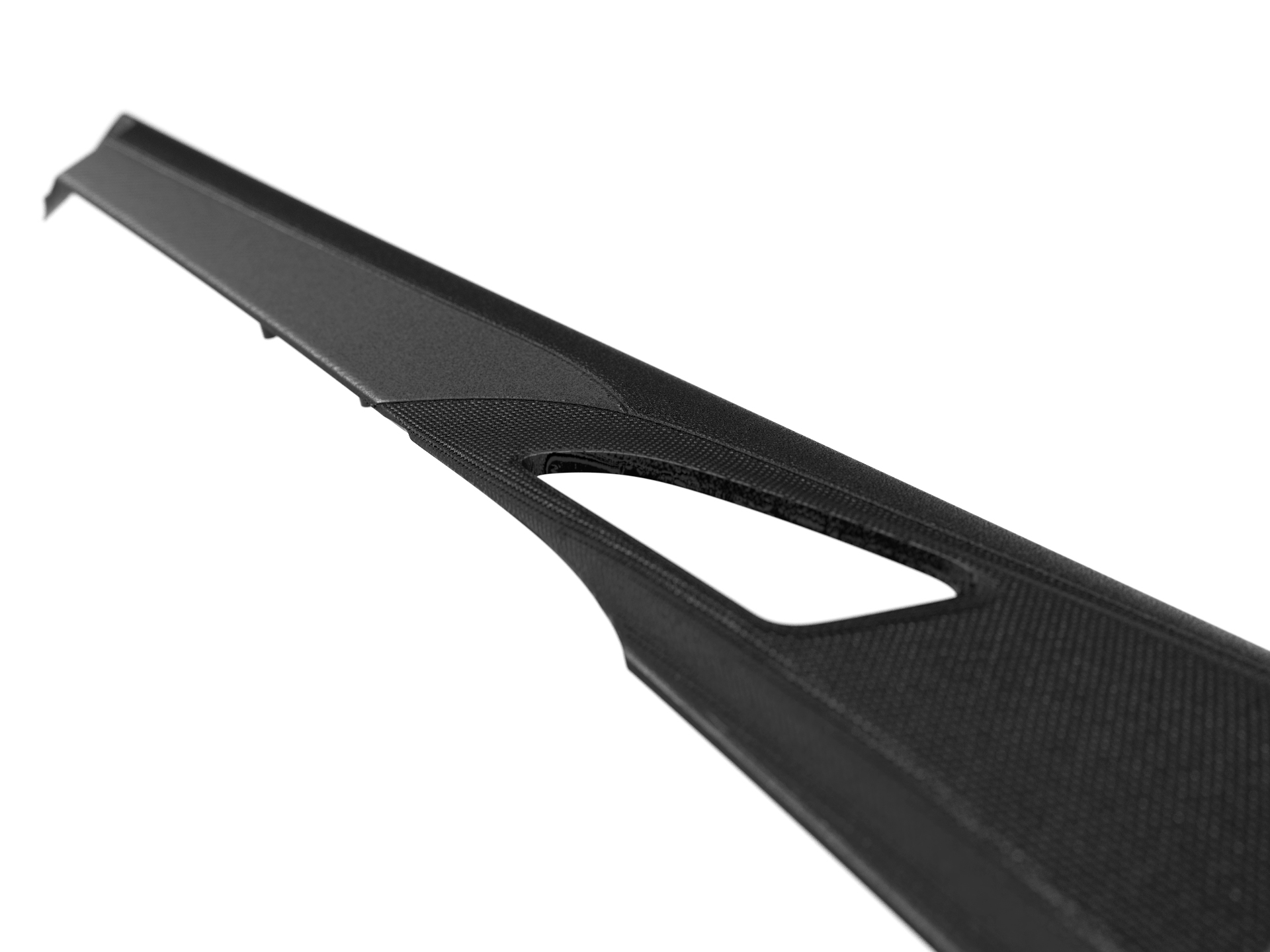
Break the Old Rules
The inherent inefficiency of conventional injection molding is the reliance on the screw to pack the cavity as the plastic solidifies and shrinks. The conventional use of the pack & hold phase imposes part design and processing limitations that the industry has accepted since its inception.
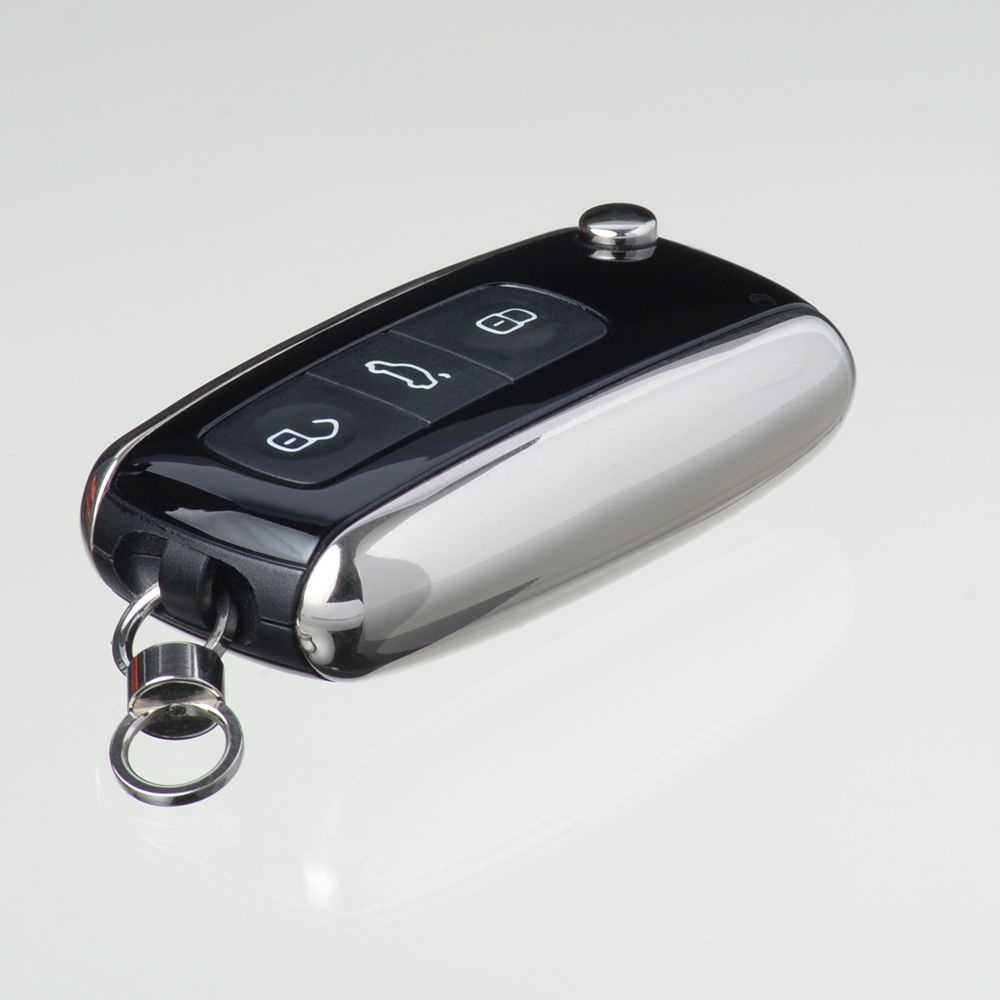
Unlock New Possibilities
MuCell® technology relies on cell growth to uniformly pack the entire cavity. Localized packing force from within the cavity unlocks processing and design freedom otherwise unobtainable through conventional holding pressure.
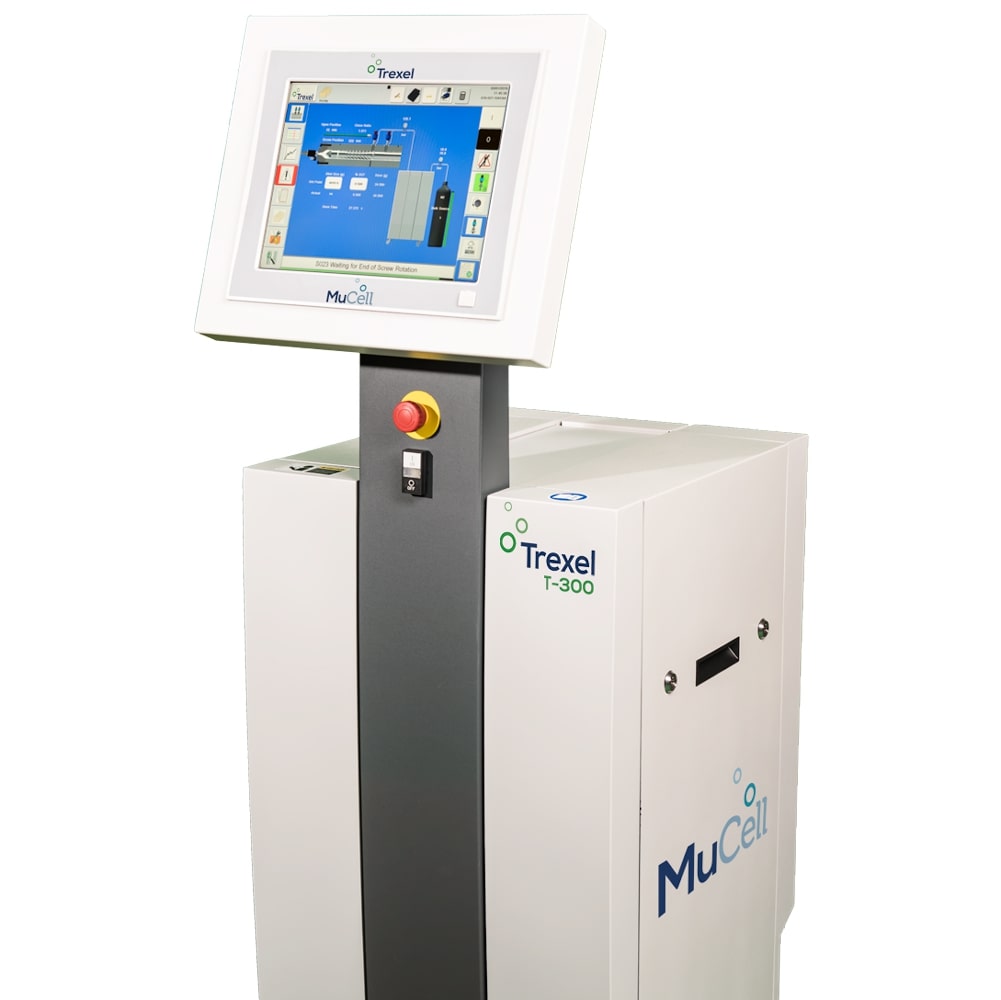
Implementing MuCell®
MuCell® is a one-time equipment purchase with no license fee.
The technology can be integrated into new injection molding machines by Trexel’s OEM partners or retrofitted into existing injection molding machines by Trexel’s field engineers.
Let’s Make it Happen
Don’t hesitate to reach out to our global team.
We’re here to assist and provide you with answers to all of your inquires. Let’s take a look at your application and discuss whether our technology can help you reduce costs AND your carbon footprint. We are eager to guide you through the process. Get in touch today!
By Phone:
781-932-0202
By Email:
info@Trexel.com