A Pöpplemann study of the last 7 years showed a significant material savings of 1,690 tons by incorporating MuCell® vs standard compact injection molding
Pöppelmann (Lohne, Germany) is a leading player in the plastics processing sector with over 700 injection molding machines, thermoforming lines, and extruders. With a focus on customer requirements and sustainable solutions, the family-run company, in operation for over 70 years, originated as a cork factory in 1949. Now employing over 2,500 across three plants in Lohne and additional locations in France, the USA, China, and sales offices in the Czech Republic, Spain, and Denmark. Pöppelmann excels in various advanced technologies, including injection molding with MuCell® technology, thermoforming, clean room manufacturing, IML, welding, FEM calculations, and simulation.
Trexel, Inc. is a leader in MuCell® microcellular foaming technology for injection and blow molding, offering design flexibility and cost savings. Their partnership with Pöppelmann began in 2006, and Trexel recently sold Pöppelmann their 26th MuCell® system.
“Quality ‘made by Pöppelmann’ is well-known in over 90 countries along with our longstanding commitment to sustainability,” states Mr. Frank Schockemöhle, Head of Technology Management. “We are proud to be the largest MuCell® customer with the most systems in operation. Incorporating MuCell® technology has been one of the tenets of our success – driving innovating solutions for our customers’ applications that provide a multitude of benefits from the foaming technology.”
Pöppelmann benefits from energy savings through a reduction in clamping force of up to 50% and the subsequent use of smaller machines to accomplish the same application. The automotive sector saw emission reductions and improved CO2 impact due to part weight reduction. Over 7 years, material savings compared to standard injection molding amounted to an impressive 1,690 tons (see table below).
“Each business division must find solutions for very specific applications – tailor-made and customized answers both to our customers’ requirements and to our demand for quality and responsible use of plastic as a material. This also includes a quality assurance manufacturing process. We are firmly convinced: If used and manufactured responsibly, plastic is the most sustainable material for many applications,” adds Schockemöhle.
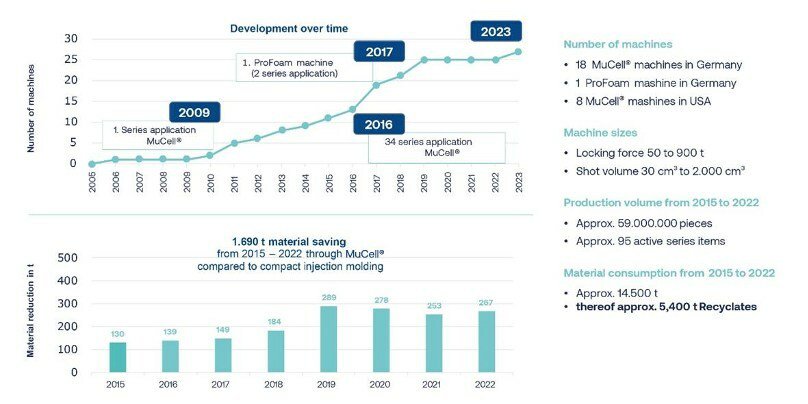
Fig.1: Top table shows quantity of MuCell® systems from 2005 to present / Lower table shows material savings by MuCell® of 1690t.
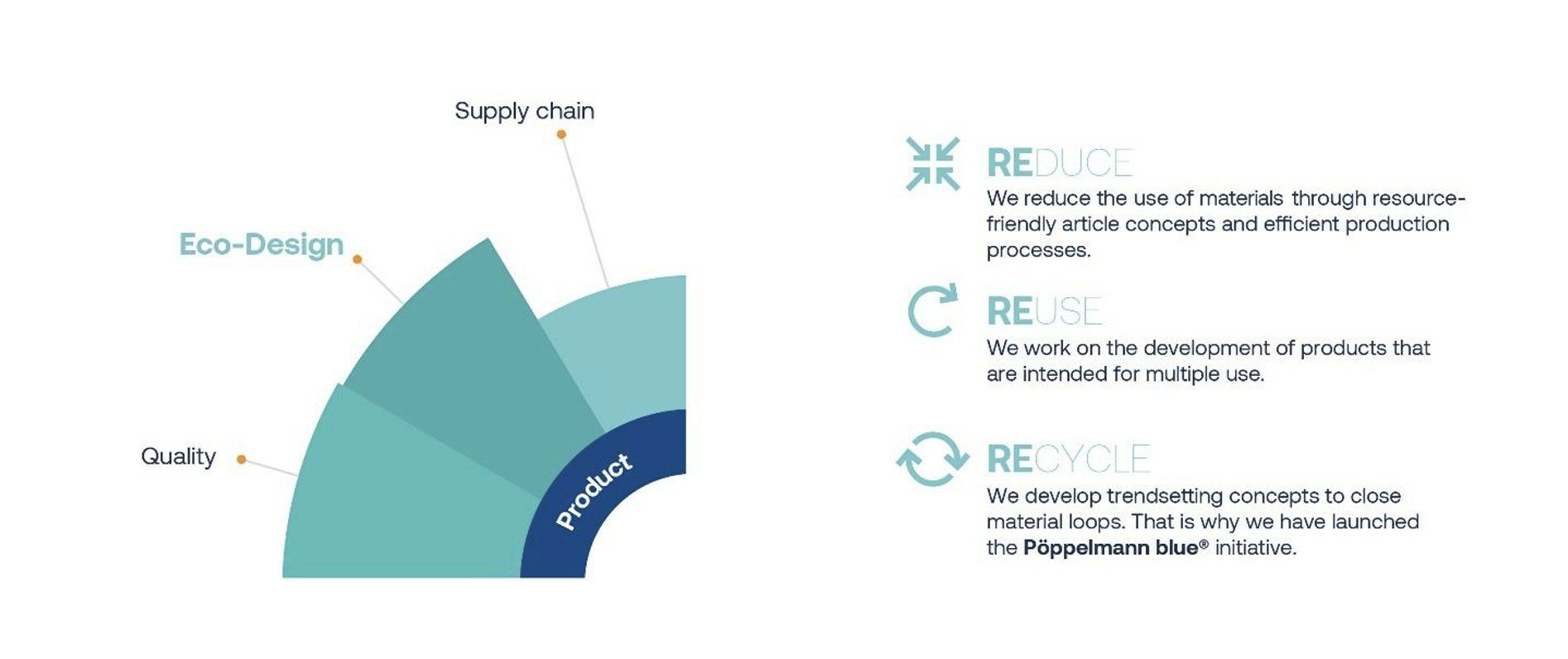
Fig. 2: Pöppelmann´s product development uses Eco-Design and contemplates the entire lifecycle