UL94 Flammability Discussion
Background – The issue of UL certification for foamed parts is an ongoing discussion point particularly for consumer electronics applications molded with the MuCell Process. There are different aspects of UL certification and the effects of foaming by physical or chemical foaming agents on a materials UL status. For the perspective of this document, we are only discussing UL94 flammability ratings.
UL94 Standard:
The UL94 standard deals with the flammability rating of plastics used for consumer devices and appliances. The standard allows for three basic testing methods, the vertical burn test, the horizontal burn test and a 5V rating.
It should be noted that the automotive industry does not typically use UL94.
Vertival Burn Test
The most common of these test methods is the standard vertical burn test. The results of which are a rating of V-0, V-1 and V-2. The test apparatus for a vertical burn test is shown below. In the vertical burn test, the test specimen is suspended vertically above a flame source.
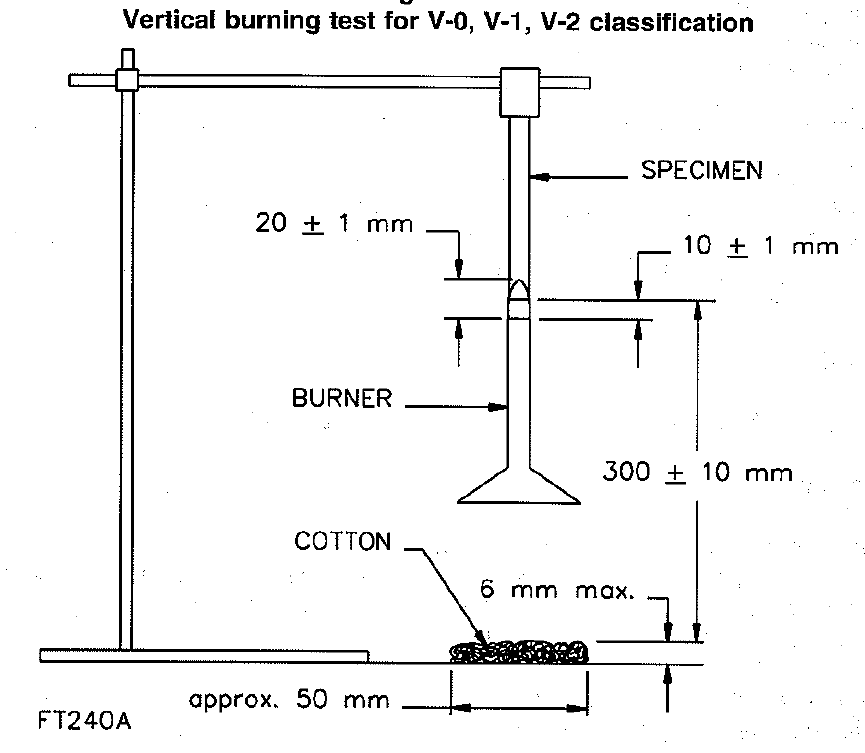
The flame is moved to within 10 mm of the bottom of the test specimen and remains in this position for 10 seconds. Once the flame extinguishes, the burner is placed back under the test specimen for an additional 10 seconds. The standard vertical burn test only requires two exposures to the burner.
The requirements for the corresponding flammability ratings are shown in the table below. If the material does not comply with any of these requirements, it is deemed to have no vertical burn rating.
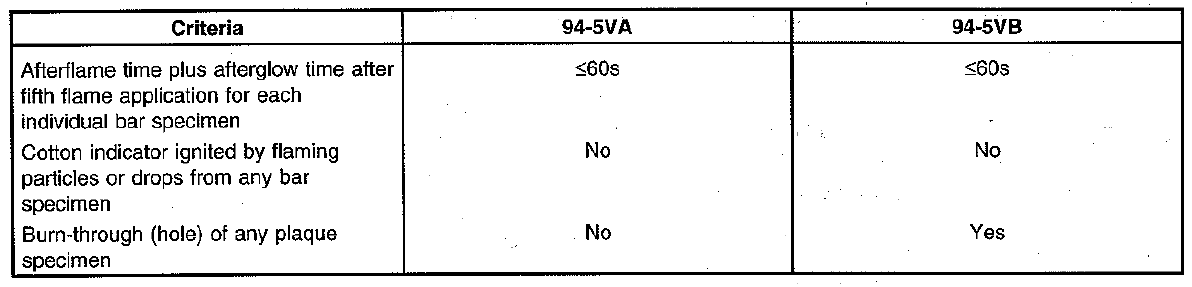
The afterflame time, t1 is the time after the burner is removed the first time until the test specimen self-extinguishes. The afterflame time, t2 is the time after the burner is removed the second time until the test specimen self-extinguishes.
Vertical burning 5V Rating
A 5V rating is based on a test specimen that is tested in the vertical configuration but is ignited 5 times. In this case the sample is exposed to the flame. After the sample self-extinguishes the flame, it is again exposed to the flame. The sample must self-extinguish each time within a predetermined time period. The requirements for a 5V rating, 5VA or 5VB, are shown below.
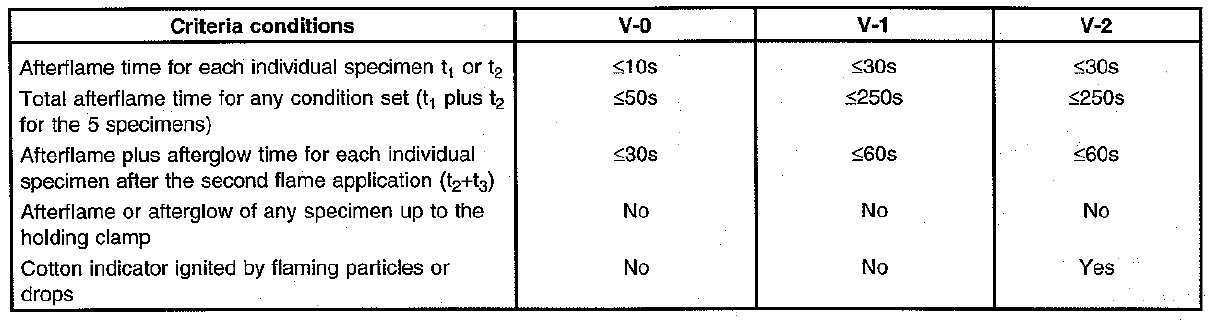
Any sample that fails to self-extinguish after the fifth application of the flame will be deemed to have failed this test.
Horizontal burn test
The horizontal burn test is less difficult and much less common than the vertical burn test. In the case of the horizontal burn test, the sample is place in a clamp horizontally and the burner is placed at one end of the sample (see below). For the horizontal burn test, the sample is exposed to the flame for 30 seconds. The rate of burn is measured starting at a line 25 mm from the unclamped end of the test specimen and a line 100 mm from the unclamped end of the test specimen.
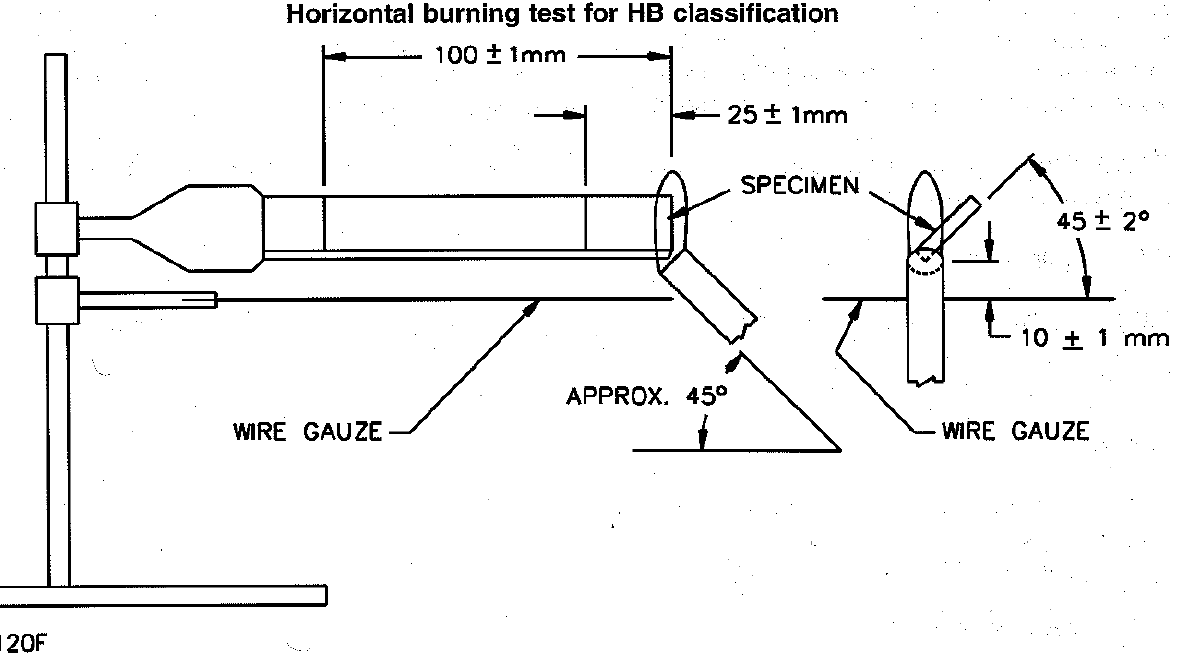
Materials tested using the horizontal burn test receive and HB rating provided:
- Burn rate of less than 40 mm/minute for a test specimen thickness between 3 mm and 13 mm
- Burn rate of less than 75 mm/minute for a test specimen thickness less than 3 mm
- Self-extinguishes at less than 100 mm burn distance.
There is a special case of the horizontal burn test for foams, that results in a rating of HBF, HF-1 or HF-2. There is not a defined density or density reduction for a material to qualify as a foamed plastic. From the perspective of Trexel’s traditional markets, this test would not be applicable.
Maintenance of UL Ratings:
The common term used is that a material receives a yellow card. This is the official UL listing with the material performance ratings. UL testing must be done on a yearly basis. There are two general ways this can be done. The first is by submitting samples to UL for testing and the second is to have testing done by a certified lab and submitting the result to UL. Ultimately the cost is about the same. At the time this work was done in 2008, the cost was $5150/material for flammability testing and then an addition cost to register the material.
Performance of Materials:
As V and 5V ratings are of most interest, the remainder of this document will focus on these. There is an existing UL exemption for foamed materials at a density reduction of less than 5%. That exemption allows for a material to maintain the compact vertical burn test rating without the need for retest. It should be noted this exemption was original implemented for chemically foamed plastics where the foaming agent was being used to eliminate sink marks. However, it is applicable to all foaming technologies. It should also be noted that this exemption does not appear to have been based on any significant testing.
A UL94 rating is based on a material and a test specimen thickness. A test specimen of 3.2 mm is assumed to represent the performance of a material at 3.2 mm thickness or greater. If approval is received at 3.2 mm, no additional testing is required on thicker test specimens. For material thicknesses less than 3.2 mm, the test specimen must be at the desired thickness and represents approval at that thickness or thicker up to the next thickness evaluated. For example, it would be possible for a material to be tested at 3.2 mm and receive a V-0 rating and also to be tested at 2.0 mm and receive a V-1 rating. This would mean that for any part with a minimum wall thickness of 3.2 mm, the material would be deemed to have a V-0 rating. However, for parts with a wall thickness between 2 mm and 3.2 mm, the material only has a V-1 rating. In addition, the material could not be used for a part that has a wall thickness of less than 2 mm as it was not tested below 2 mm.
Trexel was involved in a series of flammability tests for a manufacturer of business equipment. At that time, 5 materials were evaluated at multiple thicknesses and with multiple rounds of testing. These materials included a glass filled PBT, two unfilled PC/ABS resins, one glass filled PC/ABS resin and one mineral filled PPE/PS resin. The sample submissions and results are outlined in the table below.
The left hand column shows the material designation. The second column shows the thickness of the samples submitted for each given material. The test thicknesses for each material were picked based on existing approvals for the materials. The UL94 rating for the material in solid is given in the third column. The density reduction on the samples foamed with the MuCell process are shown in the fourth column and the column on the right shows the UL94 rating for the MuCell foamed samples. The standard UL94 test specimen is 5 inches (127 mm) in length and 0.5 inch (12.7 mm) wide. The target density reduction for each sample was 10%. In instances were the density was less than 10%, the actual value represents the maximum achieveable density reduction for the material and part configuration.
Any columns highlighted in yellow show equivalent ratings for the solid test specimens and the test specimens produced using the MuCell process.
Material | Test Thickness | Solid Material Rating | Weight Reduction | Actual Results |
1164G30 (PBT+30%GF) | 1.5mm | V0 | 10% | V0 |
1.8 mm | V0 | 11% | V0 | |
ZM3640 (Mineral filled PPE+PS) | 1.5mm | V1 | 5% | V2 |
1.8 mm | V1 | 11% | V1 | |
TN-7500MC (PC+ABS) | 1.5mm | V0 | 7.5% | V1 |
2.0 mm | V0, 5VB | 8.0% | V0, no 5VB | |
2.3 mm | V0, 5VB | 10% | V1, no 5VB | |
TN-7800MC (PC+ABS) | 1.8mm | V1 | 8% | no rating |
2.8 mm | V1 | 11% | V2 | |
DN1520HL (20% GF PC+ABS) | 2mm | V1, 5VB | 8% | no rating |
2.3 mm | V1, 5VB | 11% | no rating |
It can be seen that for the glass filled PBT, it was possible to maintain the UL rating, V-0, even at 10% density reduction down to the minimum value of 1.5 mm thickness. In the case of the other materials, it was typical to see a decrease in the result of 1 rating step. So for example, it can be seen that for the ZM3640, a talc filled modified PPE/PPO, the compact rating was V-1. At 1.8 mm, the V-1 rating was maintained but at 1.5 mm the rating was V-2. This would mean that this specific material was V-1 at 1.8 mm and thicker but V-2 between 1.5 mm and 1.8 mm.
Some samples were also submitted for 5V evaluation but in this case all foamed samples failed the testing. Note, the 5V testing was not requested on the glass filled PBT. It is not known how this material would have performed.
While there are some exceptions, in general, as the test specimen thickness decreases, the tendency to see a decrease in the UL 94 flammability rating increases both in solid and with the MuCell process. However, there is a tendency for the rating to change faster with the MuCell process.
Only one glass filled semi-crystalline resin was evaluated but this material maintained the V-0 rating even down to 1.5 mm.
With respect to the 5V testing, the most common issue was flaming material dripping onto the cotton material after multiple ignitions which is considered a failure.
Conclusions:
In general, it is expected that the flammability ratings for materials at 3.2 mm and thicker would be maintained with the MuCell process up to 10% density reduction. Below 3.2 mm, this becomes material dependent and in most cases, it should be expected that there will be a decrease of one rating step, V-0 to V-1, V-1 to V-2, V-2 to no rating. It is not expected that a foamed material will maintain a 5V rating.