MuCell® technology, also known as microcellular foam injection molding, is an innovative manufacturing process used to produce lightweight and cost-effective plastic parts. It involves the injection of a supercritical fluid (SCF), typically nitrogen or carbon dioxide, into the molten plastic during the molding process. This creates a microcellular foam structure within the plastic part, resulting in various benefits and highly accurate dosing. The latest evolution of MuCell® foaming features a smart, simple user interface with highly accurate dosing capability.
Not sure which MuCell® product is right for you? View our MuCell® Product Charts below or contact our Sales Team.
Implementing MuCell® Systems
MuCell® is a one-time equipment purchase with no license fee.
The technology can be integrated into new injection molding machines by Trexel’s OEM partners or retrofitted into existing injection molding machines by Trexel’s field engineers.
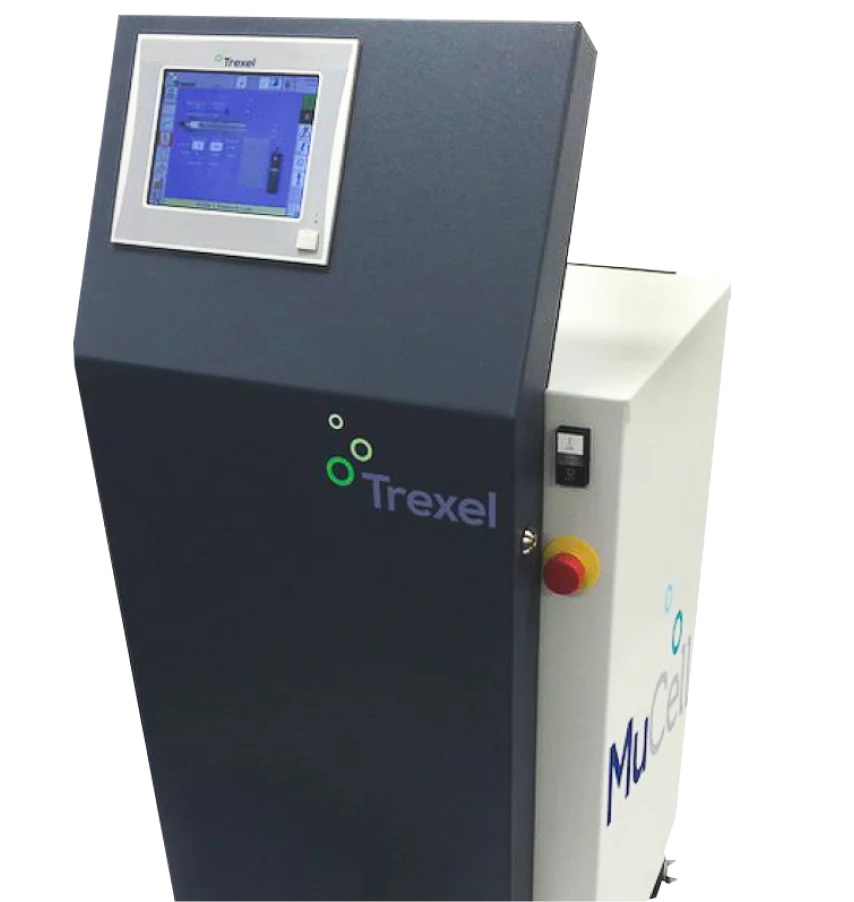
Key Advantages of MuCell® Technology
Conventional Limitations
High Molded-in Stress
Prone to Warp & Sink
High Clamp Force
Flow Length to Wall Limitation
Fill Thick to Thin
Conventional Cycle Time
Solid Density
Conventional Design & Weight
Normal Energy Consumption
MuCell® Advantages
Low Molded-in Stress
Reduced Warp & Sink
Reduced Clamp Force
Expanded Flow Length to Wall
Ability to Fill Thin to Thick
Reduced Cycle Time
Lower Density
Reduced Weight through Design Freedom
Energy Savings
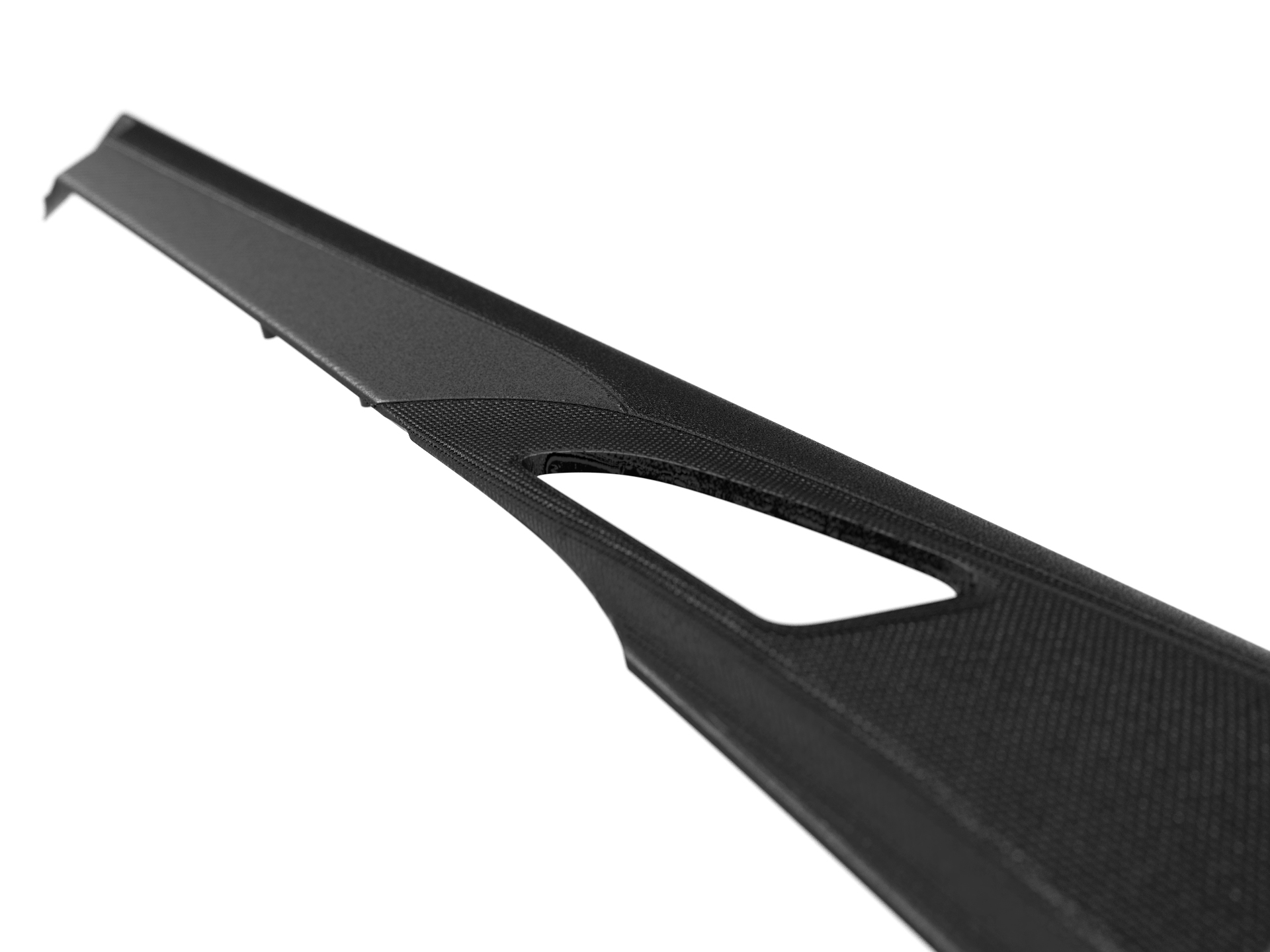
Break the Old Rules
The inherent inefficiency of conventional injection molding is the reliance on the screw to pack the cavity as the plastic solidifies and shrinks. The conventional use of the pack & hold phase imposes part design and processing limitations that the industry has accepted since its inception.
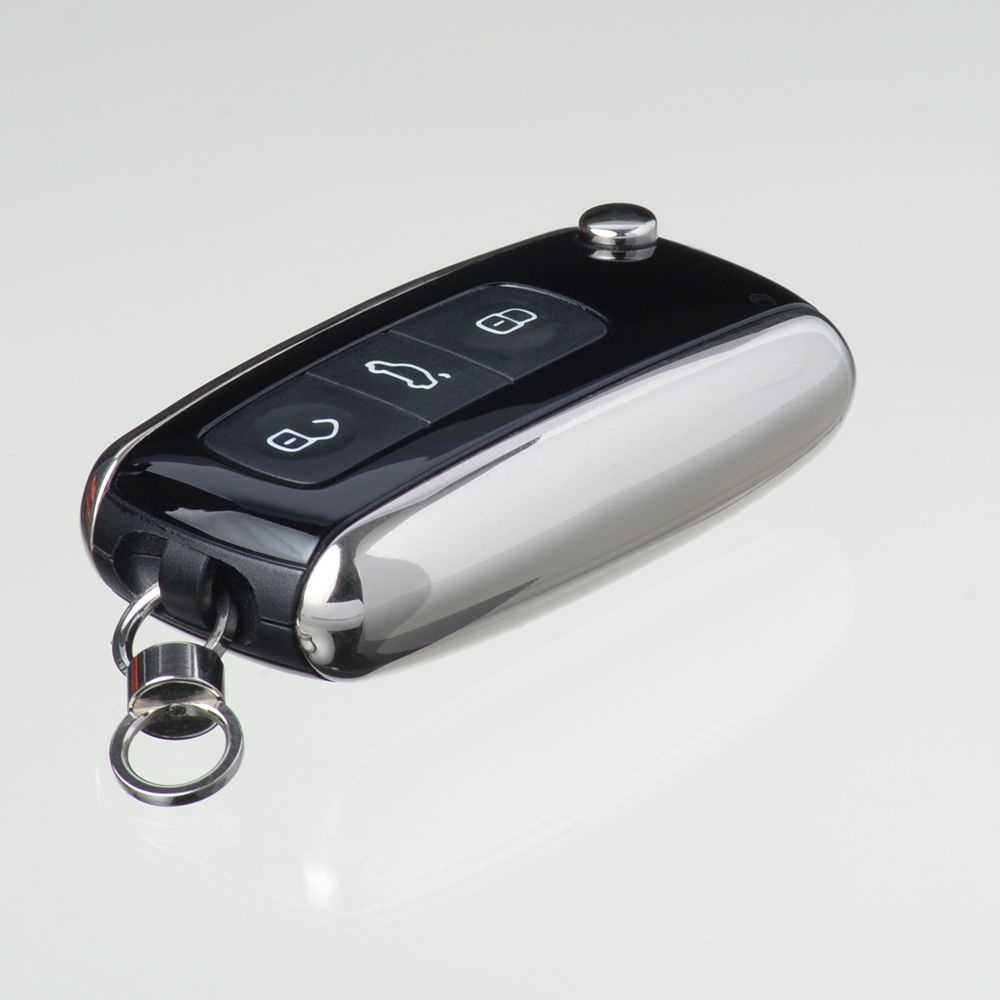
Unlock New Possibilities
MuCell® technology relies on cell growth to uniformly pack the entire cavity. Localized packing force from within the cavity unlocks processing and design freedom otherwise unobtainable through conventional holding pressure.
The MuCell® Process generally offers a 50-75% improvement in key quality measures, such as flatness, roundness, and warpage, also eliminating all sink marks. These improvements result from the fact that relatively uniform stress patterns are created in the molded part rather than non-uniform stress characteristic of conventional molding.
The quality advantages of the MuCell® Process are complemented by certain direct economic advantages, including the ability to produce 20-33% more parts per hour on a given molded machine, and the ability to mold parts on lower tonnage machines as a result of the viscosity reduction and the elimination of the packing requirement that accompanies the use of supercritical gas.
For additional information refer to the MuCell® Process Guide which explain all aspects of the process from set-up to optimizing results.
Four Technology Steps
The MuCell® process involves the highly controlled use of gas in its supercritical state to create microcellular voids in thin-wall parts. The voids are created as a result of homogeneous nucleation that occurs when a single-phase solution of polymer and gas passes through the injection gate into the mold.
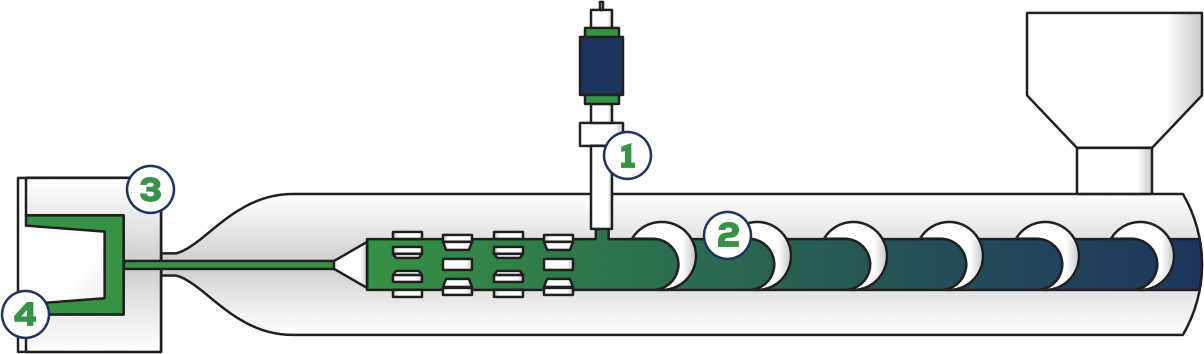
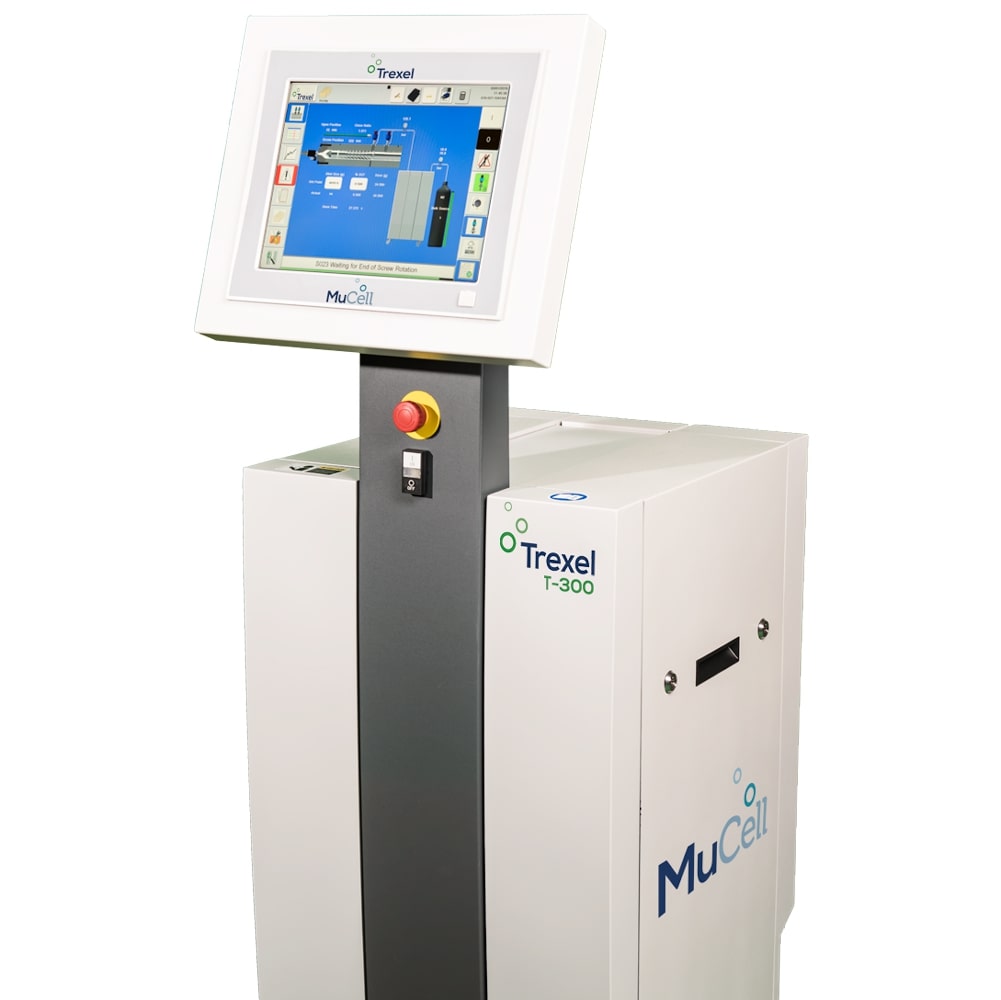
Implementing MuCell®
MuCell® is a one-time equipment purchase with no license fee.
The technology can be integrated into new injection molding machines by Trexel’s OEM partners or retrofitted into existing injection molding machines by Trexel’s field engineers.
Let’s Make it Happen
Don’t hesitate to reach out to our global team.
We’re here to assist and provide you with answers to all of your inquires. Let’s take a look at your application and discuss whether our technology can help you reduce costs AND your carbon footprint. We are eager to guide you through the process. Get in touch today!
By Phone:
781-932-0202
By Email:
info@Trexel.com